Use of 3D Printing in Implant Manufacturing
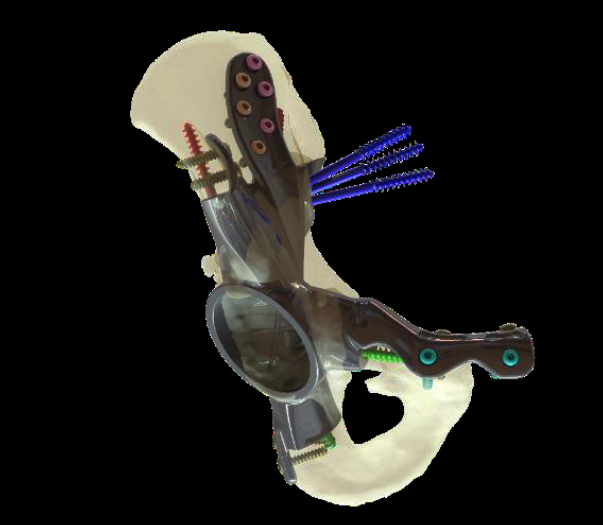
3D printing is a relatively new technology for mass and highly individualised production.
ProSpon is a member of the CZECHIMPLANT cluster, where it was also a founding member. A significant milestone in implant production was in 2015 when ProSpon purchased a 3D printer (from Concept Laser) for the 3D printing of titanium and its alloys.
With this, they have added individual implants for orthopaedic and oncological indications to their complete portfolio of manufacturing replacements for all human joints and other parts of the human skeleton. 3D printing is essential for customised individual implants where the conventional manufacturing process would be so long that it would not benefit the patient. This is particularly relevant to oncology patients, whose delay can be life-threatening. Gradually, in collaboration with universities, they have developed a system for processing titanium alloys and optimising it to make the most of this groundbreaking technology. But there are also economic considerations to be addressed. Overly expensive implants cannot be made where significantly cheaper standard machined modular systems for extensive joint replacements can be used. For individual patients with significant defects is, on the other hand, possible to use this technology excellently and effectively given the patient's condition. They have advanced both technologically and biologically, they can use porous structures that are not otherwise manufacturable, and they can program the change of implant stiffness according to the stiffness of the replaced bone.
The possibility of bone cell ingrowth into the formed pores of the base material is also essential. Another advantage of the porous 3D print is that various resorbable materials can be injected into the porous structure to allow the targeted application of antibiotics or other drugs, ensuring their gradual release.
The percentage of 3D printing, especially metal manufacturing, needs to be higher than standard technologies. Still, for extensive defects and replacements such as the pelvis, shoulder blades, shoulders and knees, it is possible to cover the manufacturing for every patient in need. 3D printers can also create replacements for oncological child patients where implants are necessary, which can protect and grow damaged limbs. The most miniature implant they have made so far is the replacement of carpal bones lunatum which also adds to the porous structures so that the tendons can grow to it. On the other hand, the largest implant can be the replacement of the pelvis part. Here the polymer material can be used not for implants but for trimming templates printed from the CT model. Thanks to them, operators can take off the same part of the bone corresponding to the printed implant.
Even though they are a small company, they try to go global with its implants. Over ten distributors are already in different parts of the World, orienting on the East market. Slowly, 3D implants are becoming a significant field of production. They also create implants for veterinary use - f.e. for dogs.
They don´t think they will expand 3D printing into the hospitals since the legislation around medical manufacturing is necessarily firm, and hospitals can´t reach the conditions. Therefore, creating implants in specialised and certified companies is much easier. The immune response to the 3D implant is the same as the reaction on the standard implants, and that is because used materials for 3D printing have the same standardised composition as for machined implants.Approving a new type of alloy would be a long run. It would take at least three years of work with multimillion expenses. Nevertheless, work is continuously being done to supplement the metal parts of the implant with other 3D printing of various biomaterials.
For easy identification, people with implants are issued with so-called implant cards, both for treatment in another country and for passage through security frames, e.g. at the airport, which allows them to travel by plane without problems.
Zdenek Cejka
ProSpon, spol. s r.o.
![]() |
Created: 24/11/2022 13:50:13
|
![]() |
Created: 24/11/2022 13:53:30
|